Modular Construction: A Sustainable Solution for KSA’s Green Buildings
Modular construction, also known as prefabricated or off-site construction, is gaining traction in the Kingdom of Saudi Arabia (KSA) due to its numerous benefits.
This innovative construction method involves building various components or modules of a structure off-site in a controlled factory setting and assembling them on-site like Lego pieces. This approach differs from traditional construction, where each element is built on-site from scratch.
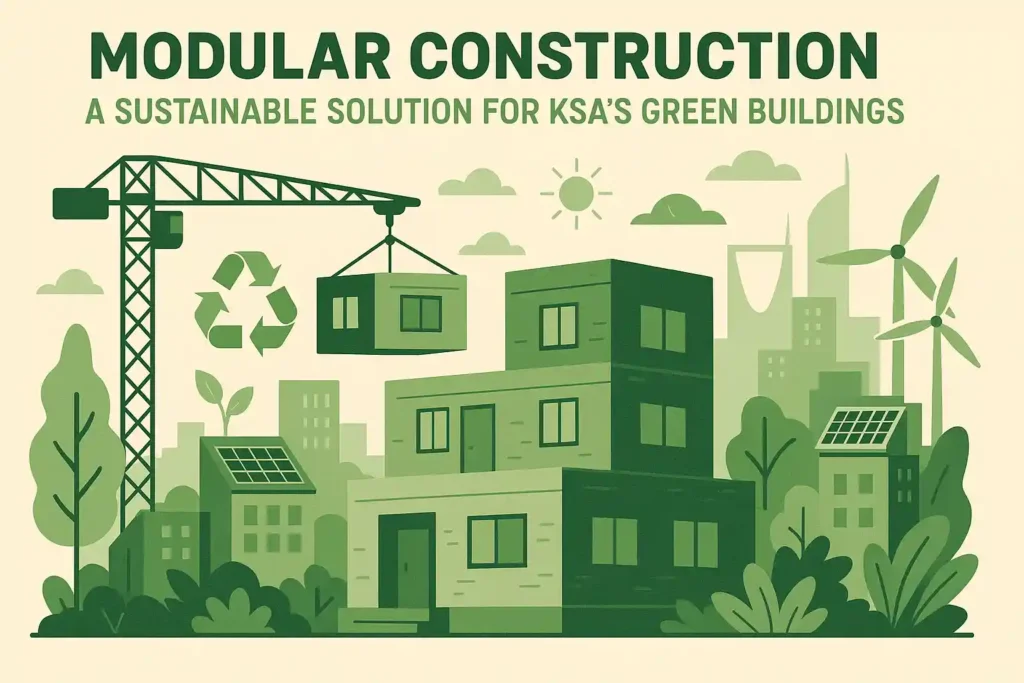
The construction market in KSA is expected to reach USD 28.27 billion by 2026, with a compound annual growth rate of 5.8% from 2021 to 2026.
This staggering growth is driven by the government’s efforts to reduce waste and accelerate green building projects to achieve its ambitious Vision 2030 goals. In this article, we will delve into the impact of construction on reducing waste and accelerating green building projects in KSA.
Reducing Waste with Construction
Modular Construction and demolition waste are significant contributors to landfill waste, accounting for about 50% of global landfill waste and 90% of debris in developing countries. In KSA, the construction industry produces an average of 55 million tons of waste annually, with only 20% being recycled.
This is where construction proves to be a game-changer. By utilizing construction techniques, modules are manufactured in a factory setting, resulting in significantly less waste compared to traditional construction.
In construction, all scraps, sawdust, and unused materials are easily collected and recycled within the factory, ensuring minimal waste. This approach eliminates the need for on-site dumpster rentals and frequent debris removal, reducing waste on-site and enhancing cleanliness and safety throughout the construction process.
Additionally, the assembly-line-style production of construction in a controlled factory environment ensures efficient material use and waste reduction. Each module in construction is carefully measured, cut, and assembled with precision, significantly minimizing material wastage when compared to conventional on-site construction.
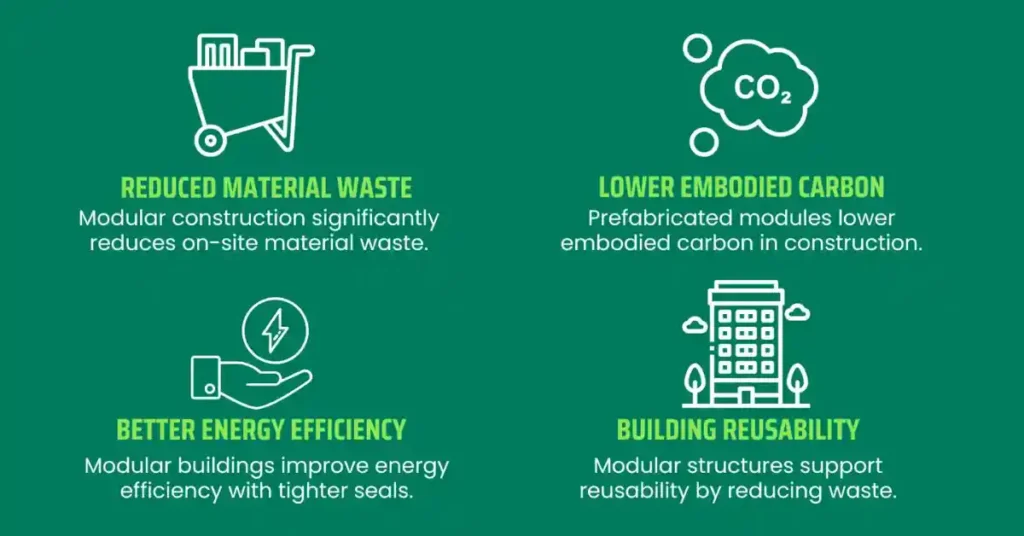
Additionally, since the building process is streamlined and standardized, the likelihood of errors and re-work is reduced, further reducing waste. Furthermore, the construction process generates fewer harmful emissions on-site, contributing to a cleaner and healthier environment.
In traditional construction, heavy machinery and equipment release toxic pollutants, such as carbon monoxide and nitrogen oxide, into the air. These emissions can negatively impact the environment and workers’ health.
With construction, the majority of the building work is done off-site, minimizing the use of heavy machinery on-site, resulting in lower emissions and a more sustainable construction process.
Accelerating Green Building Projects in Construction
The KSA government has set ambitious goals to promote sustainable development and reduce the country’s carbon footprint through its Vision 2030 plan. One of the key pillars of this plan is energy efficiency and green building.
The modular construction method is a perfect fit for these goals as it offers various benefits that accelerate green building projects.
Firstly, construction is more energy-efficient than traditional construction.
Modules are built to be highly insulated, reducing heat transfer and making them more energy-efficient.
This insulation helps lower energy consumption in the long run, thereby reducing carbon emissions.
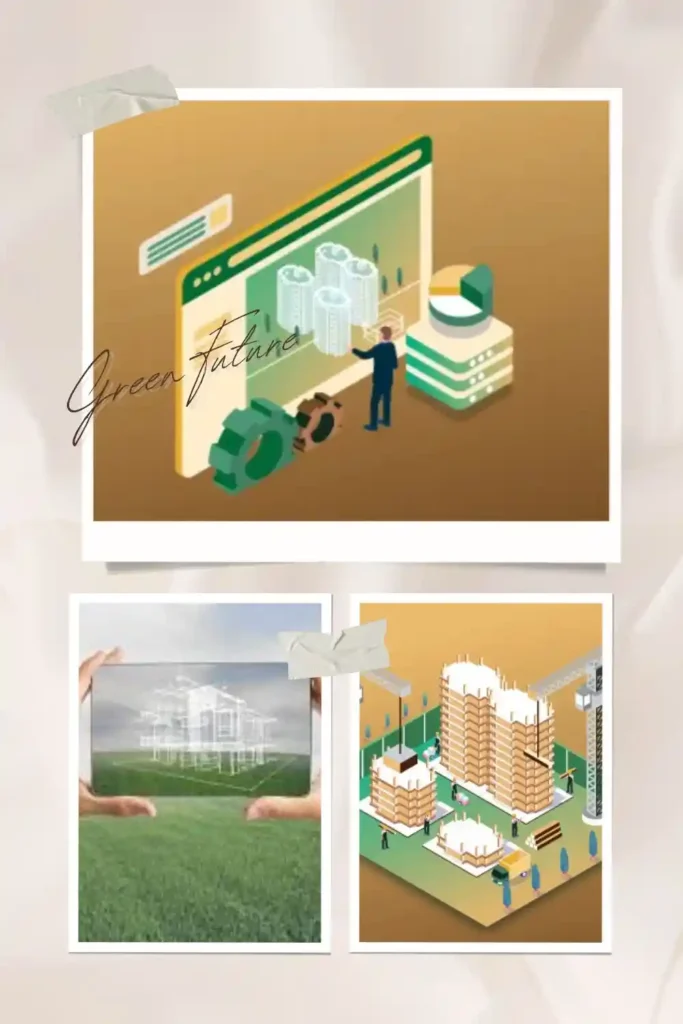
Furthermore, the factory setting allows for efficient recycling of unused materials, reducing the need for new material production, which is energy-intensive. Moreover, the controlled factory environment enables the use of green building materials and techniques, ensuring sustainable and eco-friendly construction.
For instance, construction allows for the use of recycled steel, bamboo, and other sustainable materials, promoting a circular economy and reducing the reliance on traditional building materials that have a high impact on the environment.
Additionally, since modules are produced in a controlled factory, there is no exposure to adverse weather conditions, preventing any damage to the building material and ensuring a longer lifespan of the structure.
Conclusion
construction is proving to be a transformative approach for the construction industry in the Kingdom of Saudi Arabia, aligning with the nation’s Vision 2030 goals. By reducing waste, increasing efficiency, and promoting the use of sustainable materials, construction offers a clear path towards more environmentally-friendly and energy-efficient building practices.
With its ability to streamline the construction process, reduce emissions, and facilitate faster project delivery, construction is accelerating the growth of green building projects in KSA.
As the market continues to expand, this innovative method is set to play a key role in shaping the future of sustainable development in the region.
This Construction can save up to 20% to 30% in costs due to reduced material wastage, faster project completion, and fewer disruptions to the construction site, leading to lower labor costs.
FAQs
1. What is Modular Construction?
Modular construction is an innovative building method where components are prefabricated off-site in a controlled factory environment and then assembled on-site, similar to putting together a puzzle.
2. How does Construction reduce waste?
construction minimizes waste by creating modules in a factory, where materials are precisely measured, cut, and assembled. This approach results in less material wastage compared to traditional on-site construction methods.
3. What are the benefits of Construction for green building projects?
construction supports green building by improving energy efficiency, using sustainable materials, and reducing the carbon footprint through controlled production and efficient recycling of materials.
4. Is Construction more cost-effective than traditional building methods?
Yes, construction can be more cost-effective due to its efficient production process, reduced labor costs, and minimized material waste, making it a more affordable option for both residential and commercial projects.
5. Can Construction be used for large-scale projects?
Yes, construction is highly scalable and can be used for various types of large-scale projects, including residential buildings, commercial structures, and even entire communities.
6. How does Construction contribute to energy efficiency?
construction allows for highly insulated modules, reducing heat transfer and lowering energy consumption, which makes buildings more energy-efficient in the long term.
7. How does the assembly process of Modular Construction work?
In modular construction, individual modules are built off-site in a factory setting. Once completed, these modules are transported to the site and assembled into the final structure, reducing construction time and disruptions.
8. Is Modular Construction a sustainable building solution?
Yes, modular construction is sustainable because it reduces material waste, uses energy-efficient methods, and often incorporates recycled or eco-friendly materials, making it an environmentally responsible choice for construction projects.
9. How does Modular Construction help meet Vision 2030 goals in KSA?
Modular construction plays a significant role in achieving the KSA Vision 2030 goals by promoting sustainable construction practices, reducing waste, and accelerating the development of energy-efficient green buildings across the Kingdom.
10. Does Modular Construction require special permits or regulations?
Modular construction may require different permits and regulations depending on the location and scale of the project. However, it is subject to the same building codes and standards as traditional construction, ensuring safety and compliance.